
What will manufacturing and labor look like in a decade?
Once AI and robotics are in full bloom, once production and services are full digitized, dematerialized, demonetized, and democratized, what happens to how and where you work? To our global economy?
The disruption of the global supply chains and the labor market during the COVID-19 pandemic began a global shift towards onshoring manufacturing and offshoring labor.
The use of robotics, 3D printing, and advanced automation has allowed Western companies to “onshore” production at a reasonable cost, shifting away from lower-cost labor in Asia, in favor of “owning their local supply chain” using low-cost automation.
At the same time, collaboration technologies such as Zoom, Teams, and Slack are allowing companies to offshore their talent, expanding access to highly sought-after experts globally.
In today’s blog, we’ll discuss the future of manufacturing and labor, the Metatrend that will remake the global economy and reshape global business.
Let’s dive in!
(This blog is written by Peter H. Diamandis, MD and Cheo Rose-Washington)
WHAT CAUSED THE SUPPLY CHAIN CRISIS?
The COVID-19 pandemic affected 98% of global supply chains.
Why is that such a big deal?
Because the global supply chain is a key driver of economic activity around the world and it plays a critical role in connecting countries and facilitating trade, innovation, and growth. According to the UN, the global trade of merchandise goods is worth more than $25 trillion.
But the disruptions caused by the pandemic led to shortages in nearly everything that needs to be produced or manufactured—from electronics and toys to chemicals and running shoes.
As the New York Times reported, shortages beget more shortages: “A paint manufacturer that needs 27 chemicals to make its products may be able to buy all but one, but that one — perhaps stuck on a container ship off Southern California — may be enough to halt production.”
For example, shipping a container of goods from China to the US generally requires a month, but this time frame tripled during the height of the pandemic. At the same time, the cost of making that trip ballooned: sending a 40-foot container from Asia to the US went from $1,326 in August 2019 to over $18,000 in August 2021.
The economic effects were immediate, widespread, and in some cases devastating to business.
In 2020, 64% of companies with revenues greater than $1 billion reported losses between 6% and 20%. One estimate puts the total lost revenue during that year at $4 trillion dollars.
More than COVID-19
Yet the direct effects of the pandemic, including lockdowns in China, haven’t been the only factors affecting the global supply chain.
Geopolitical events such as trade tensions between the US and China and the Russia-Ukraine conflict have also led to disruptions.
The ongoing shortage of semiconductor chips, which continues to affect over 160 industries, illustrates the impact of these multiple forces on the global supply chain.
In early 2020, the pandemic caused massive disruptions to the semiconductor supply chain and logistics, just as we saw a 13% increase in global demand for PCs as people worked from home. Later that year, trade tensions between the US and China heated up, followed by soaring demand for cryptocurrencies, which require massive amounts of data mining, into 2021.
Severe weather events in Taiwan, the world’s leading producer of chips, led to further disruptions in 2021.
Finally, Russia’s invasion of Ukraine further exacerbated this. Ukraine’s two leading producers of neon, a key component of the lasers used to make chips, produce half the world’s supply of neon. And both producers halted operations once the conflict started.
This “perfect storm” of factors disrupting the global supply chain has caused two things to occur:
(1) Western companies bringing their manufacturing capacity closer to home
(2) The growing adoption of industrial robots and 3D printing to increase efficiencies while reducing costs
Let’s explore each trend in turn…
ONSHORING: A PARADIGM SHIFT IN MANUFACTURING
Onshoring, also called reshoring, refers to the process of bringing manufacturing capacity located in a foreign country back to the home country where the business’s products are sold.
For years, the main reason why companies based their manufacturing in China or India was cost savings—to take advantage of the lower labor costs in those countries.
But as living standards in China and India are on the rise, so are labor costs there. For example, wages in the manufacturing sector in China have more than tripled during the past decade.
The result is that keeping manufacturing based there is less cost-effective.
In fact, even when onshoring manufacturing may not be the lowest-cost option, many companies are beginning to see it as the “best-cost” option when they consider supply chain dependability and resilience.
Using low-cost labor overseas may improve profit margins, but if the supply chain breaks due to a pandemic, geopolitical events, or some other factor, then there is no profit margin because there are no products to sell.
Here are 4 ways that onshoring is helping to address global supply chain issues:
(1) Improved Quality Control: With their operations closer to home, companies have more control over their manufacturing process and can better monitor their products. A survey by the Reshoring Institute found that 60% of companies that have reshored their operations have seen quality improvements.
(2) Reduced Shipping Costs: Having operations closer to end consumers also means that companies can reduce shipping, storage, and handling costs. The same Reshoring Institute study found that 40% of companies saw reductions in shipping costs.
(3) Increased Speed to Market: No longer relying on overseas suppliers means that companies can bring their products to market faster. According to the Boston Consulting Group, companies that onshore operations can bring products to market up to 20% faster.
(4) Domestic Job Creation: Onshoring also leads to more jobs in the home country, as companies invest in new manufacturing operations and equipment. For example, according to the Reshoring Institute job announcements for reshoring initiatives hit a record high of roughly 350,000 in 2022, up from 250,000 in 2021 and 150,000 in 2020.
Evidence of the growing trend of onshoring is all around us:
-
According to the Kearney Reshoring Index, 92% of CEOs have expressed positive sentiments toward reshoring. And 79% of executives with manufacturing capacity in China have already moved part of their manufacturing capacity to the US or plan to in the next 3 years.
-
A 2022 Bloomberg report found that construction of new US manufacturing facilities has increased by 116%.
-
Semiconductor chip factories have opened in New York, and semiconductor companies have announced new facilities in the Midwest.
-
Major US retailers, including Walmart, have vowed to spend hundreds of billions of dollars over the next 10 years on goods produced domestically.
-
A combination of billion-dollar federal and state support in the US is aimed at encouraging domestic manufacturing, as part of the Biden Administration’s plan to revitalize American manufacturing.
Just as more manufacturing is being onshored, robotics and 3D printing are further reducing costs and increasing efficiencies…
HOW ROBOTICS & 3D PRINTING ARE DISRUPTING MANUFACTURING
With labor rates increasing, political issues mounting, and the lingering effects of the pandemic continuing to disrupt supply chains, we can provide lower-cost labor—and ultimately lower-cost manufacturing—through robotics and 3D printing.
Robotics
As companies consider the tradeoffs between keeping their manufacturing facilities abroad or onshoring them, robotics and automation are helping to tip the scales in favor of onshoring.
The OECD has found that robotics adoption correlates with declines in offshoring. For example, in developed economies, a 10% increase in robotics applications results in negative 0.54% growth in offshoring.
A decade ago, these multimillion-dollar machines were so dangerous they were walled off from the workforce behind bulletproof glass and so complicated to program that PhDs were typically required.
Not anymore.
McKinsey’s 2022 Global Industrial Robotics Survey shows that companies across the industrial world are betting big on robotics and automation, with automated systems projected to account for 25% of capital spending over the next 5 years.
A separate analysis by McKinsey estimates that installations of industrial robots jumped from 450,000 a year in 2015 to 600,000 last year.
Here are 4 benefits that industrial robots bring to manufacturing:
(1) Lower Costs: Robots can perform tasks more efficiently than human labor, which can result in lower labor costs. Despite an estimated cost of $250,000 for a sophisticated industrial robotic arm, a company can reach breakeven with traditional labor costs in less than 2 years. Over the last 30 years, the average robot price has fallen by more than 50% in real terms while labor costs have increased over 100%.
(2) Increased Productivity: Industrial robots can work 24/7 without breaks, leading to increased production rates. They don’t go on strike and they don’t have health issues. According to the International Federation of Robotics, industrial robots increased productivity by 30% in the automotive industry between 2010 and 2015.
(3) Improved Quality: Robots can perform repetitive tasks with high accuracy and consistency, resulting in a lower defect rate. For example, a study by the National Institute of Standards and Technology found that robots reduced the defect rate in the electronics industry by 75%.
(4) Improved Safety: Robots can perform hazardous tasks, reducing the risk of injury to human workers. For example, the U.S. Bureau of Labor Statistics reported that the injury rate in the automotive industry declined 85% between 1991 and 2015.
3D Printing
3D printing is about to transform manufacturing as we know it, decimating waste, multiplying speed to market, and harnessing never-before-used materials.
Already valued at over $12 billion in value, additive manufacturing products and services are projected to reach more than $70 billion by 2030.
The original 3D printers showed up back in the eighties. They were clunky, slow, hard to program, and easy to break, and only printed plastic.
Today, the machines have colonized most of the periodic table. We can now print in hundreds of different materials, in full color—in metals, rubber, plastic, glass, concrete, and even in organic materials such as cells, leather, and chocolate. And what we can now print is getting increasingly impressive. From jet engines to apartment complexes to circuit boards to prosthetic limbs, 3D printers are fabricating enormously complex devices in increasingly shorter time frames.”
This is a big deal for industry. The on-demand nature of 3D printers removes the need for inventory and everything that inventory demands.
Other than the space required for feedstock materials and the printer itself, the technology all but erases supply chains, transportation networks, stock rooms, warehouses, and all the rest.
This one development, a single exponential technology, threatens the entire $16 trillion manufacturing sector.
And fast. Until the early 2000s, 3D printers were exceptionally pricey machines in the hundred-thousand-dollar range. Today, they can be purchased for under $1,000.
As prices have dropped, performance has increased, and convergences have begun to arise—moving 3D printing into a wider variety of markets.
For example, early in the pandemic emerged as a stopgap solution. Between February and July 2020, companies with 3D capabilities, 3D printing enthusiasts, and hospitals printed nearly 40 million face shield parts, 12 million nasal swabs, and 116,000 ventilator parts.
And 3D printing has continued to take off since then, spurred in part by the Biden Administration's Additive Manufacturing Forward initiative to improve supply chain resilience.
A few examples:
-
The US Air Force is 3D printing metal replacement parts as needed, instead of relying on costly inventory or waiting years for parts made with hard-to-source components.
-
GE’s 3D-printed fuel nozzle for commercial airplane engines is made with 1 component—instead of 20 individual components, resulting in cost savings of 30% and a new nozzle that is 25% lighter and 5 times more durable.
Here are 5 benefits that 3D printing brings to the manufacturing industry:
(1) Decreased Lead Times: 3D printing significantly reduces lead times for production, because it eliminates the need for tooling and molds, and enables on-demand production. According to Accenture, the average lead time for 3D printing production is just 24 hours, compared to traditional manufacturing methods, which can take up to several weeks.
(2) Increased Flexibility: 3D printing allows for more flexible and decentralized production, which can help mitigate the effects of disruptions in the supply chain. The technology allows companies to maintain production despite supply chain disruptions.
(3) Lower Shipping Costs: Because it allows for production closer to the point of consumption and sale, 3D printing also reduces shipping costs. This leads to lower transportation costs, reduced carbon emissions, and billions in cost savings.
(4) Improved Product Customization: 3D printing allows highly customized products, which can improve customer satisfaction and lead to increased demand for products.
(5) Increased Resilience: By reducing dependence on single suppliers, 3D printing also helps to increase the resilience of the overall supply chain. McKinsey estimates that 3D printing can reduce supply chain risk by 50%.
OFFSHORING LABOR – ACCESS TO GLOBAL TALENT
The COVID-19 pandemic had a profound impact on work culture and how businesses operate. And the convergence of 5G networks, AI, VR, AR and the metaverse will continue the disruption and reinvention of the workplace.
With the acceleration of remote work and the exploding growth and adoption of digital collaboration tools like Slack, Zoom, and Teams, people can increasingly live and work anywhere.
At the same time, companies are now gaining access to talented and low-cost labor anywhere on the planet.
Just as we’re onshoring manufacturing and supply chains, we’re offshoring talent.
Offshoring talent is the process of relocating business activities (e.g., customer support, software development) to employees who are living in another country, someplace where the labor and other resources are cheaper.
For example, on average a US analyst earns a salary of $110,000, whereas that same role in India earns less than $15,000. Think of it as geographic arbitrage.
I personally have employed AI and coding experts from Central and South America, Ukraine, Poland, and the Philippines just to name a few regions of the world. Typically, the talent is as good as those from Silicon Valley, sometimes even more motivated and often 20% or 30% of the going rate.
All these forces are combining to create a global business environment that looks very different than what existed before the pandemic.
Here are 6 implications of post-COVID work and business:
(1) Growth of Remote Work: The pandemic forced companies to adopt remote work models on an unprecedented scale. As the US Census Bureau notes, the number of people primarily working from home tripled between 2019 and 2021. At the same time, companies have increasingly tapped into this larger pool of remote workers to reduce costs associated with physical office space and other overhead expenses.
(2) Geography Becomes Irrelevant: Digital networking technologies have largely made geography irrelevant. The Economist points out: “Companies may gain more flexibility to seek out new workers for new tasks in new places. Portugal has created a visa for digital nomads, who will be able to work from the country for a year. Argentina wants to introduce a preferential exchange rate for freelance workers selling their services abroad.”
(3) Geographic Arbitrage: There is a huge geographic arbitrage for global talent where a company can access, for example, top AI scientists and developers in Asia, Central and South America, or Eastern Europe. For instance, according to a 2022 GitHub study there are 10 million developers in India, where the average salary for a developer is under $8,000 (compared to roughly $110,000 in the US). Both Poland and Romania have seen massive influxes of developers and other IT professionals following Russia’s invasion of Ukraine. And the number of developers in Latin America is 1 million, with half of them in Brazil.
(4) Growth of Hybrid Operating Models: Companies are developing new “operating methodologies” such as 85% remote work / 15% in-person work. Currently, 74% of US companies use a hybrid working model or are planning to implement one, including Amazon, Apple, Google, Microsoft, 3M, and other large companies.
(5) Gig Work Becomes More Common: Another trend that has emerged as a result of the pandemic is the increase of gig workers and other independent contractors. For example, workforce management firm MBO Partners estimates that the number of American workers engaged in independent work for at least 15 hours a week increased from 15 million in 2019 to 22 million in 2022. As The Economist notes, “Gig work is no longer just about ride-hailing or food delivery. Upwork specializes in web development; Fiverr is known for media production. Amazon turned to Tongal, another freelancing platform, when it needed a team to rapidly produce social-media content for its Prime TV shows.”
(6) The Metaverse Gains Momentum: Face-to-face and immersive working sessions still have significant value compared to Zoom exhaustion. But next-generation metaverse-AI environments will take this to a new level in the next 2 to 3 years. The metaverse, which could be worth $13 trillion and have 5 billion users by 2030, will transform how we live and work, impacting every industry: from retail and advertising to education and entertainment. Within the metaverse, we can all live in different locations, but work “co-geographically” in a shared virtual space. One example is Vatom, a metaverse platform recently used by Google to bring together over 10,000 employees in an immersive digital environment where they interacted and engaged in a free-flowing fashion.
FINAL THOUGHTS
The COVID-19 pandemic has accelerated the already rapid adoption of exponential tech—and in the process it’s transformed global commerce and how we live and work.
If you can shrink your supply chain and manufacture your products locally and on-demand, how does that change your business model?
Now that you can access a global pool of talent, how will the structure of your company change?
For example, does it make sense to hire full-time people in California when you can find similar—or even superior—talent at significantly lower-costs in Brazil, India, or Poland?
Business models and industries that can’t adapt to the new environment caused by the pandemic will continue to go extinct.
This opens up massive opportunities for agile entrepreneurs to capitalize on this rapidly changing environment.
Remember: every crisis yields entrepreneurial opportunities.
In our final blog in the Metatrends series (#20 of 20), we’ll explore Increasing Global Abundance.
DOWNLOAD MY FREE METATRENDS REPORT
Are you interested in what I think is *most important* for entrepreneurs, creatives, and leaders to understand over the next 10 years?
Download a free copy of my full report: Top 20 Metatrends & Moonshots Report for 2022 - 2032.
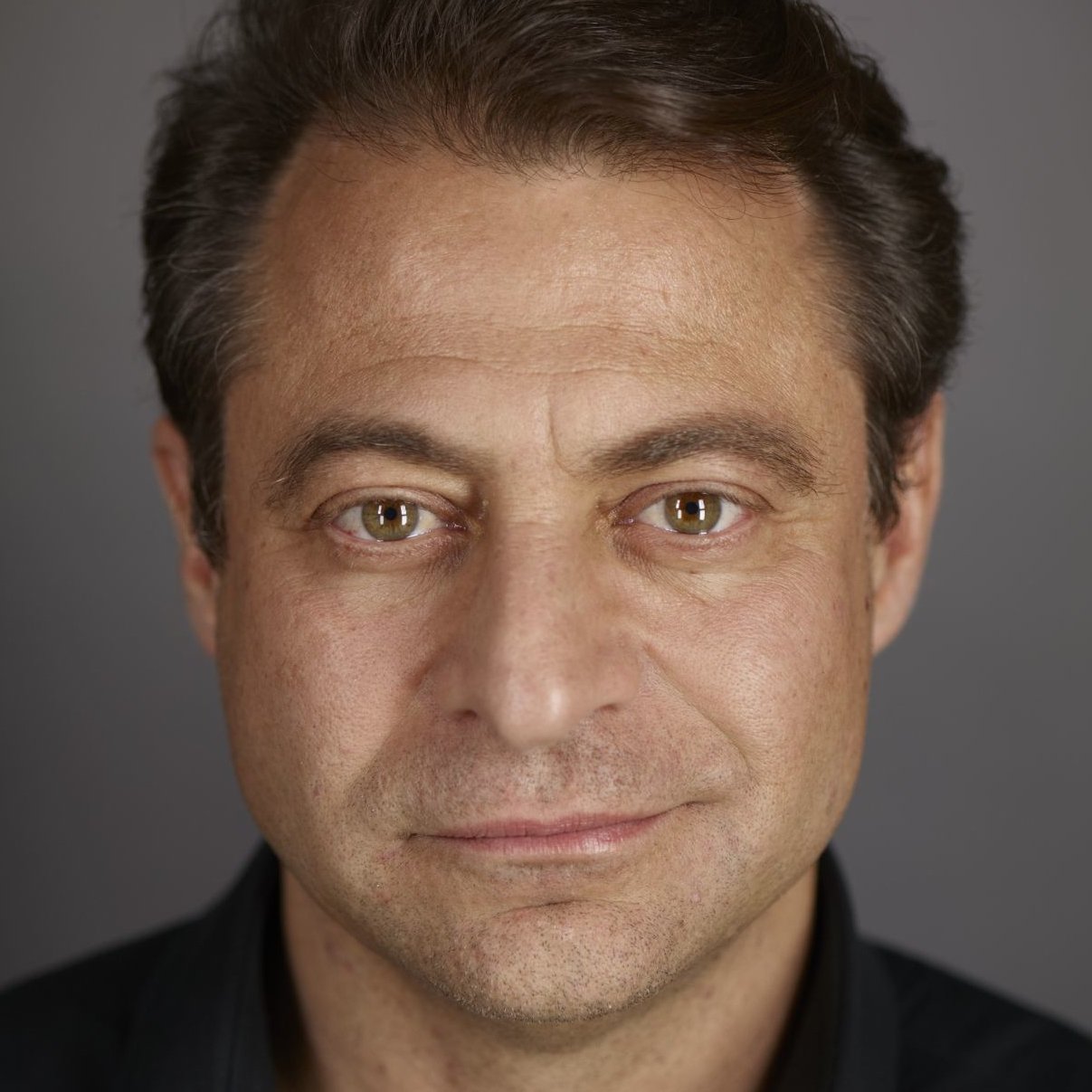